检测、生产、设计...质量到底是怎么来的?不论是史上的多位质量大师,还是范围缩小到我们制药行业内部的众多科研工作者,对于如何把控质量大关,一直在学习并加以寻找着更为真实的答案!药品质量体系,涉及多个方面多个维度,可以说任何“点”都存在一定的风险系数,而今天要说的“工艺验证”问题,绝对可以说是任务量较大,且须长期关注的一大块问题。
1.工艺验证~概念更新及发展
·最早源于美国cGMPCFR21类210~211部分的要求;
·1987年FDA《工艺验证总则指南》对工艺验证进行了定义~即“建立证明文档,高度确保某一工艺能连续不断的生产满足预先制定的规范和质量品质的产品”;
·WHO对生产工艺验证的定义~“能够证实任何程序,生产过程、设备、物料,活动或系统确实能导致预期结果的有文件和记录的行为”;
·2008年FDA再次发布工艺验证指南(草案),对工艺验证的概念和文件要求进行了大幅度地修改和更新;
·我国2010版GMP对工艺验证的定义为“在工艺设计至商业化生产的过程中收集以及评估数据,这些数据是该工艺能够持续稳定的生产出符合质量要求产品的依据”,同时指南也指出工艺验证的目标是保证“同批产品的同质性及不同批产品之间的一致性”;
·2011年FDA发布工艺验证指南正式版《ProcessValidation:GeneralPrinciplesandPractices》;
·2015年中国CFDA发布《药品生产质量管理规范(2010年修订)》确认与验证附录,在第六章中明确工艺验证应包括首次验证、影响产品质量的重大变更后的验证、必要的再验证以及在产品生命周期中的持续工艺确认,以确保工艺始终处于验证状态...
2.工艺验证~目的&意义
由以上FDA、WHO及我国药监系统对于“工艺验证”的概念的定义,不难分析出工艺验证的目的和意义。
一方面,对确保产品质量起重要作用,而质量保证的基本原则是生产出的产品符合其预定用途。工艺验证需要达到一定的质量目的,如产品的质量、安全性和有效性必须是在设计和生产中得到的;质量不是通过检测或检验成品得到的;必须对生产过程中的每一步骤加以控制,以使产品符合质量和设计的所有标准的几率达到最高;只有对生产过程及质量控制进行适当的设计和验证,药品生产企业才能持续生产出合格的药品,等等。
另一方面,多个指南均要求,工艺性能与产品质量监控系统需应用于整个产品生命周期。企业一旦实施工艺验证理念,在产品开发中须及时收集数据并进行评价,在确认阶段对工艺设计进行评估。在日常生产中对工艺的持续性进行评估,对于企业建立可靠的工艺、确保稳定的质量、持续不断地供货于患者是非常有益的。
3.工艺验证~具体方法
无论是新版GMP,还是指南,工艺验证通常分3个阶段展开讨论,即工艺设计阶段、工艺确认阶段、持续的工艺审核阶段。
阶段1~工艺设计
该阶段,基于在工艺摸索及工艺放大活动中所积累的数据信息,商业化生产工艺被确定下来。该阶段主要是在实验室或者车间小规模进行,所以可以不遵循GMP的要求。这个阶段的重点,即预测、发现、检测及控制“不易控制的或者容易失控的参数”~抓住“变异”。而抓住变异,无外乎理解工艺本身所具有的的特点和对商业生产时所处环境、设施、设备、公用工程等对工艺的综合考虑。
☆主要任务:找出变异,评估变异对产品质量的影响程度,然后再制定规程监控变异。
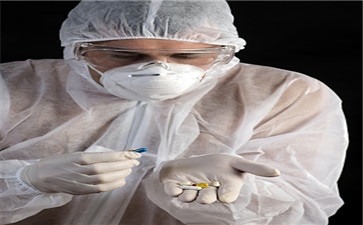
阶段2~工艺确认
该阶段,评估所设计的工艺以确定其在商业化生产条件下是否具有重现性。这个阶段已经脱离了实验室或者中试阶段了,其批量、生产环境、设备、公用设施等应均为大生产条件,故而必须满足GMP要求。通常我们要先确认厂房设施、工艺用设备、公用工程是否能够达到工艺要求,这是工艺验证的前提条件。厂房设施、工艺用设备、公用工程确认结束就可以开展工艺验证了。大多数情况下工艺验证离不开高密度的取样、额外的测试、高频率的检查或者持续监控。
☆主要任务:在厂房设施、工艺用设备、公用工程确认成功的基础上开展工艺验证,工艺验证中根据批量、工艺复杂程度、对工艺理解程度、相似产品的经验进行取样测试,并对测试结果进行对比分析。
阶段3~持续的工艺审核
该阶段,收集和评估所有生产中的信息与数据以评估工艺一直处在验证状态。这个阶段的产品已经开始上市销售,所以必须是满足GMP要求的。这个阶段数据汇总非常重要,如原辅料的质量情况、中间体质量情况、成品质量情况、每个生产步骤工艺、设备参数的变异情况、生产中的偏差、用户投诉、OOS等,从而分析出工艺的总体趋势。
☆主要任务:不断收集各种工艺数据,持续改进!
(附图:图片源于CNKI)
4.工艺验证~认识不足
即使完成以上操作,工艺验证在实际执行中,可以说各方面都存在问题。整体来说,仅有少数人员认为企业了解并深入执行了工艺验证概念,大部分人员仍认为企业并未了解工艺验证的意义。这也从另一方面说明,我国大部分制药企业仍停留在老的工艺验证阶段,并未从根本上理解工艺验证的含义。而企业方面,在综合考虑成本、人员、时间、设备、场地等各方面问题时,即使对工艺验证非常重视,但通常还是会按照最低要求去做。
在执行工艺验证过程中,大部分人员认为存在以下问题:验证前的工艺性能确认不充分(并未将风险因素考虑详尽)、只考虑3个验证批(都按着最低要求列计划)、并未执行持续工艺验证(尤其是上市后,都在尽可能的“不出问题”)。且再进一步从细节上谈,大部分人员甚至是关键岗位人员,对验证工艺、设备、政策并不熟悉,验证过程中操作人员不该存在的操作失误频发,且出现问题后并不会从验证的失败中积累经验,等等等等...
5.小结/小感
举个真实发生的例子,笔者身边所经历的一个品种,工艺验证整整做了11批。是计划列了11批吗?不是!是出问题了!然后前前后后整整做了11批,项目耽误了半年。相信参与验证环节的同行,也一定经历过类似的验证。GMP体系要求着产品的稳定,要求着体系的稳定,而这些稳定的前提,需要做非常庞大的设计工作,但我们面临的大部分问题却是,赶进度拼速度省环节。而同样有着GMP要求的外资企业,给我们最大的印象就是,在薪资令人向往的背景下,要求极为严格,可随时接受飞检。而此刻,再反观国内制药企业,有多少真正达到了GMP的要求?又有多少企业敢说自己的体系没有问题!
全文相关数据来源:药智数据、FDA、WHO、国内指南、CNKI
点击下图,预登记观展
发表评论 取消回复